What puts the giddy-up in Adrian Landon's Mechanical Horse? An…
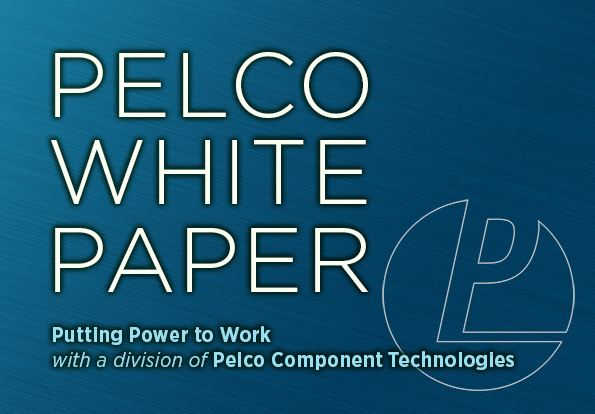
Simplified GUI and precision controls for complex CNC manufacturing
Schleicher develops streamlined programming, open system control and monitor functions, and simplified GUI for complex CNC manufacturing. See how Schleicher’s innovations meet MICROMAT’s needs.
Precision grinding with graphical monitoring
Precision machine tools in the manufacturing industry keep getting faster and more precise. As the technologies in industries served (aviation, aerospace, marine and automotive) become increasingly complex, the operation of these precision machine tools must remain simple. With this goal, MIKROMAT, a world-leading manufacturer of precision machine tools, relies on the controls of Schleicher Electronic Berlin in its thread grinding machines.
KEY CONCEPTS Automation Manufacturing Graphical User InterfaceHistory of CNC at MIKROMAT
CNC Input
CNC Monitoring
Industry 4.0
In the domain of precision manufacturing, CNC machines have replaced manually operated machine tools for a long time. These days, operation is achieved via an electronic box and computer programs, rather than manually via levers, cranks and handwheels. In this way the machines can be adjusted and monitored with considerably more precision. The truth is that the classic CNC programming via G-Code is complicated and cumbersome: each program step must be entered individually, manually, in the input screen of the HMI device. Up to 1,000 lines of hand-typed commands quickly come together. In addition, the classic CNC control panel is confusing, as it is composed of countless buttons with various letters, numerals, characters and symbols.
This is why MIKROMAT adapted its thread grinding machines 26 years ago. Here, the handling of the user interface was a decisive criterion. “Simple operation is important for our customers, so that a smooth flow, in addition to a precise result, is guaranteed,” comments Gerd Schäfer, the sales manager at MIKROMAT and the person responsible for the thread grinding application technology.
Technical possibilities and application requirements
Up until 2009, MIKROMAT, just like the other industry giants, still ran on a DOS-based system (including the G-series grinding machines), because it was a proven operating system. However, this offered no future-proof use in the long run; it was outdated and no longer able to run on today’s computer systems. “Therefore, we switched to a Windows-based system,” said Gerd Schäfer. “It is only thanks to this system that the common graphical user interface standards that exist today are achievable.”
Given the new generation of the system, MIKROMAT also had to find a new and reliable control system. After all, grinding machines are required to meet especially high standards regarding dimensional accuracy and complexity. In order to meet the specified basic size and the required accuracy in the manufacturing process, and to prevent erroneous grinding processes, a clear and easy-to-understand control operation is required. But the user interface of the updated CNC technology is a major challenge for inexperienced users in particular; they need to be trained in how to use the machine first. For this reason, in order to ensure a quick and easy incorporation, MIKROMAT placed special emphasis on monitoring, whose user interface works via insertion in a drawing template. In addition, as many tools as possible should be created, and the user should find these understandable and easy to operate. Another important criterion was the implementation within an open system. Gerd Schäfer adds, “We have clients in various industries and with various requirements . . . With an open system, we can program the monitoring individually, according to our customers‘ visions.”
Visual options with configuration
With these requirements for the new monitoring system, the search began for an appropriately potent supplier. The choice: the control manufacturer Schleicher Electronic Berlin GmbH. A decisive criterion was the open system which Schleicher can enable with its monitoring system XCA 1277. This provides MIKROMAT with an enormous range of design freedoms: the user interface can be modeled on the drawings of the technologies with the end client. The control functions are thus precisely matched to its requirements. To date, no other controller manufacturer for thread grinding machines can offer such creative freedom.
In addition, the XCA 1277 is extremely easy to use: all grinding and access data can be easily inserted in the screens, without any need for programming skills. Any language barriers will be overcome by internationally understandable imagery. “Our grinding machines are used in Russia, China and Europe, but many of our end clients don’t speak English,” says Schäfer. “For this reason, we use graphics, and as little text as possible.”
Highly modern and well-tried
Another advantage of XCA monitoring: the program can be input even when the machine is running. This means that the workflow can be significantly shortened. Additionally, the XCA 1277 is a high performance controller with enormous computing power, meaning that many interpolating axes can be monitored. Thanks to the Ethernet connection of the Schleicher monitoring system, the internal integration of the machine in the company’s technical process is also assured, making the system an ideal module for Industry 4.0 applications.
A Schleicher control system was also used in the predecessor version of the thread grinding machine. “In our XCA we have combined tried and tested functions with the most modern configuration requirements,” said Sven Dübbers, CEO of Schleicher Electronic. However, the integrated Embedded System is new. It enables communication via a PC while the CNC monitoring runs in real time on a separate core. The resulting technological options, together with the open surface design, allow for a more effective and universal use of these MIKROMAT machines.
About SchleicherUSA
Schleicher Electronic GmbH is a leading provider of automation and control solutions. In 2015 a working relationship was formed between Schleicher and Pelco Component Technologies, becoming SchleicherUSA Automation and Safety Solutions. High-performance offerings from SchleicherUSA include safety relays, measurement and monitoring relays, sophisticated time controls and switching relays, and future-proof open system machine automation products.
For product orders or inquiries in North America or Central America,
contact sales@schleicherusa.com
or phone 800-321-9539
pelcocaz.com